A Double-Knee Tilt-Over Mast
for Testing Light Antennas
Note: the tilt-over mast assembly that follows was designed to serve a special need of mine. I present the construction of it as a bag of ideas. However, several materials are pressed close to safety margins, so I cannot recommend the assembly as is to anyone else for reproduction. Some of the ideas–if carefully engineered to your needs and required safety margins–might be useful: hence, these notes.
Each year, I build and test 3 to 4 antennas for 10 meters and up (VHF). I used to use 20′ of mast that I could push up to a house bracket for short-term tests. However, in the last 10 years, trees have grown to the point of interacting with the antennas, and I needed a new test fixture.
My requirements were these:
- 1. 30′ height
- 2. Easy raising and lowering of the antenna for adjustments and revisions.
- 3. Easy assembly and disassembly of the test mast system.
- 4. Parts that can be easily and inexpensively replaced upon any signs of wear.
What I came up with suits my needs, but pushes some of the materials to their limits. The final test fixture is a double-knee tilt-over mast using common materials. Assembly requires only a few wrenches to tighten some nuts and bolts. During assembly, disassembly, and use, no bolt that needs adjustment or installation is higher than 5′ off the ground, which means that I do not need to use a ladder, with all of its inherent instability.
In a nutshell, the assembly consists of three main items. The first major part is an 8′ 4×4 pressure-treated post rooted 2.5-3 feet in the ground and stabilized with concrete. A hand winch attaches to the post bottom just above the ground. The second portion is a cradle composed of 2 pieces of 8′ long 1.25×6 decking lumber, also pressure treated. The pieces bolt to the post and have a 2×4 spine above post level. The cradle swivels on its top post-bolt for further assembly work before I raise it into its working vertical position. At its top of the cradle is a further bolt-hole for the mast assembly.
The mast assembly is the last of the three major items in the overall fixture. The lower 10′ mast section is attached to a sturdy U-channel piece as a pivot near the top of the tube. A second mast section attaches to the lower section before the cradle and partial mast assembly are raised via the winch. With the cradle vertical and bolted, the mast is lowered and the final top section is attached. Finally, the antenna is attached to the top of the mast and raised (and lowered) by the winch. Disassembly is simply the reverse of assembly. When horizontal, the antenna and mast are supported by a wide stand made from 2x4s that has been in service here for about 15 years without signs of aging.
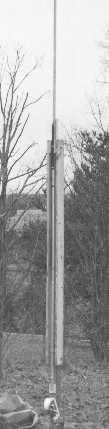
Photographs of the mast during assembly and testing accompany these notes to clarify some of the basic ideas and the sketches. Photo 1 shows the pieces of the assembly laid out on the ground and Photo 2 shows the lonely post before assembly. (Since the post is the only permanent yard addition, it will have a 4-way bracket on top to hold hanging flower baskets when I am not testing an antenna.)
Sorry but the two links to Photo1 and Photo 2 are no longer available due to the site not being active anymore.
Now for some details. I shall work from the post on up in a series of sketches. They do not show all detail, but will give a sense of what goes where.
The Post and the Cradle
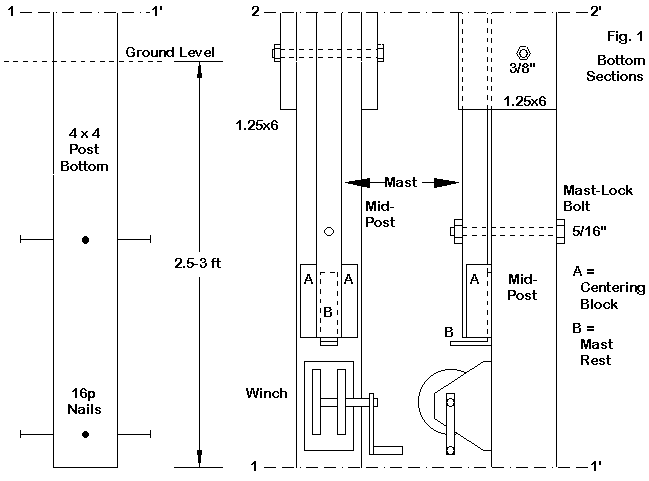
Figure 1 shows the post up to the base of the cradle. 2.5 to 3 feet of the post are below ground. Bagged concrete fills the bottom of the hole. The 16-penny nails can be replaced by any other extensions to lock the post and the concrete together. Use standard fence- post techniques to keep the post plumb while the concrete sets. I filled only about two- thirds of the hole with concrete, and added soil and grass on top. Should I ever move to a South Sea island, I can saw off the post below turf level, as if it never existed.
Just above ground level is a hand winch. Mine has a 1400 lb maximum rating, more than enough for my needs. Be sure to mount the winch to give the handle good clearance from the ground and to allow easy access to the lock. My winch required 3 bolts through the post for mounting. Every hole drilled into a vertical support piece must be carefully scrutinized as a possible weakening of the structure. However, my winch has a thick back plate and the bolts (with large washers at their heads) likely strengthen the post at the mounting point.
Just above the winch is where the lower mast section terminates. Note the centering blocks marked A in Figure 1. As the winch reaches full pull-in, the mast section may not be centered, and a pair of 1×1 block about 6″ long take any side sway out of the mast. Also note the modified L-bracket marked B in Figure 1. It acts as a mast rest, which limits the stress on the mast pivot bolt when the mast is vertical. The end of the L-bracket has been cut off and used near the top of the post as a spacer so that the mast is always as plumb as the post.
The 5/16″ by 6″ bolt above the blocks goes through a hole on the mast. When winching in the mast, it settles over the bolt and is locked with a wing-nut. I chose a wing nut as the fastest way to secure the mast to the post. A locking nut (with nylon insert) can be added for longer term on-the-air tests with an antenna.
Not shown in the sketch are two details at the bottom of the mast. One is a 1″ eye-bolt that has a use I shall note at the end of the description. The other is a piece of 1/16″ thick, 1″ wide aluminum strip, about 2″ long. It fits under the eye-bolt nut directly under the eye itself and is rolled into a J toward the mast end. It is better to roll the stock before cutting the longer strip from which this piece is made.
The only function of the strip is to keep the loop at the end of the winch rope from falling off the mast when the winch stress in relieved (after raising to the vertical or before lowering the mast). Otherwise, under raising and lowering stress, the loop rests against the eye-bolt. I use 5/16″ rope on the winch, which has proven adequate for the task so far, but steel winching cable would be stronger (and safer).
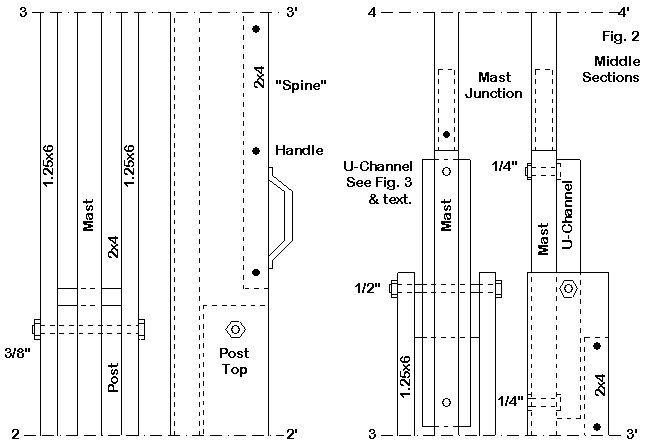
As we move up the post another 2 feet or so, we encounter the bottom of the cradle. A 3/8 by 6″ bolt secures the bottom of the cradle to the post when vertical. If we combine Figure 1 and Figure 2, we can get front and side views of the cradle and how it goes together with the post. The cradle consists of two pieces of 1.25×6 decking lumber. Three feet of this lumber overlaps the post. A second 3/8 by 6″ bolt secures the cradle to the post top and acts as a pivot during assembly.
Above the post, with clearance to pivot, is a 2×4 (also pressure treated) that provides a spine for the cradle. The spine ends about 5-6 inches below the top of the two planks and is fastened by a series of decking screws. I put in the spine for three major reasons. First, it provides a convenient place to attach the carrying handle (for toting between the storage place in my shop and the mast site). Second, it spaces and stiffens the two planks for their task in carrying the mast load. Third, it reduces the chances of the planks curving with time as the lumber ages.
Photo 3 shows the cradle in its horizontal position, before I added the first two mast sections. By resting the top end of the cradle on the antenna support, I can lift the lower end into position and tap the upper bolt through the holes. Incidentally, when assembling the structure, I always wear a jacket with accessible pockets or a carpenter’s apron. I keep the tools (wrenches and hammer) on one side and only the hardware (bolts, nuts, and washers) on the other–and only for the assembly step in progress. I keep a spare washer and nut in case of fumbling. This allows me to complete a full step with my eye on the assembly and to find the tool or hardware I need by feel alone.
Once I have the cradle in its horizontal position and bolted securely, but not tight, I add the lower mast section. The lower section sits in the cradle, with its pivot near the top. One item not shown in the sketches is the addition of two 5.5×5.5 inch plates of 3/4″ stock on the insides of the planks. This stock reduces the play of the mast mount from side to side. Since I installed it cross grain to the planks (with more decking screws), it reduces the wear rate of the pivot hole for the mast.
The Mast and the Channel
The pivot assembly for the mast consists of two pieces of perforated steel L-stock, as shown in Figure 3.
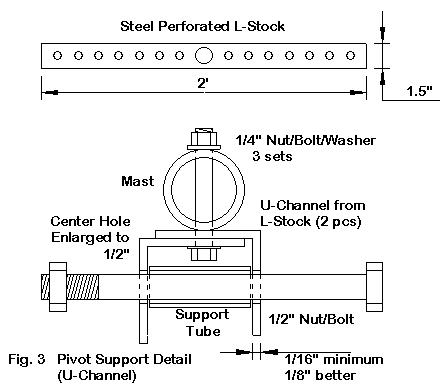
There are various grades of steel perforated L-stock available in home centers, and I have found some variability of stiffness among stock in different stores, even though they are marked as having the same thickness. Use stiff stock or change materials to something adequate to the task. This material bear the brunt of lifting and lowering stresses in the assembly. A welded assembly would be stronger, but my aim was to have something that nuts and bolts could handle.
A pair of 2′ sections of the L-stock combine to form a single U-channel. The pivot bolt is a 1/2 by 6″ unit, which requires enlarging the existing center hole along the length of stock. I placed one piece inside the other while drilling to ensure that the final holes aligned in a level way when I reversed one piece to form the U-channel.
Photo 4 shows the actual assembly. The mast mounts on the flat double surface with three 1/4 x 2″ bolt and nut sets–one centered and the others near the ends of the assembly. Although not shown in Fig. 3, I added a strip of 1/6″ steel strip, 1″ wide and as long as the U-channel. This strip sits on top of the mast with three holes for the bolts. These holes are drilled as accurately as possible so that the strip resists any tendency of the mast to stretch the top surface when under load, that is, when horizontal. Masting is not designed to be drilled and then stressed at the hole positions, and metal fatigue is a distinct potential. Hence, any holes should be reinforced in appropriate ways. Lock washers and nuts secure the assembly.
Between the side surfaces of the U-Channel at the pivot point, I added a steel tube that prevents inward collapse of the channel. (Further reinforcement was added at a later stage of construction.) The 1/2 x 6″ bolt passes through the doubled side planks, through the channel and tube, and out the other side, to be secured with a washer and lock nut. I have also used a wing nut for quick tests.
Once the lower mast section is in place, I attach the winch and tighten it without lifting the cradle and mast section. I move the antenna support further outward and add the second mast section. To pin the mast, I drilled a hole through the junction and added a #10 self-tapping screw. The sole function of this screw is to keep the mast sections from sliding apart when I add an antenna to the mast top while it is angled downward. The screw should bear no load during lifting and use.
The next step is to raise the cradle and two mast sections with the winch and lock the mast in place. Then, returning to Figure 2, I insert the lower cradle bolt and tighten down both the upper and lower bolts. The cradle pivot has finished its task until time to disassemble the mast.
Releasing the mast lock (removing the wing nut), I then lower the mast only. The assembly is sufficiently balanced that the winch can support the two masts at an angle that is proper for the next step. I move the antenna support further out and rest the top mast section on it while joining it to the middle mast section. Again, a sheet metal screw prevents the new section from sliding out when I add an antenna load.
Photo 5 shows the masts fully joined and secured in the down position. The mast sections required for this work must be heavy duty material–as heavy duty as you can obtain. Lighter masting is available, but will likely collapse as soon as you try to lift an antenna into position. The 20′ of mast beyond the pivot point will present a near-limit load under their own weight unless the steel masting is thick enough to support itself horizontally. Even the heavy duty Radio Shack masting that I have used for over a dozen years will have a severe load limit that I shall discuss below.
Remember: collapsing masts can cause severe injuries. They create an element of surprise that freezes you in place momentarily, and that delay can produce special dangers. Use strong materials and every other applicable safety precaution when using such a mast system.
The semi-final product–minus any antenna–appears in Photo 6 on the left, fully winched up and locked. Besides the missing antenna, this photo–taken during initial testing–also is minus the clamp and guy ring, along with the trailing guy ropes. Whenever I intend to use an antenna for extended on-the-air tests, I always guy the mast with the ring about 2 feet below the antenna.
Lifting and Loads
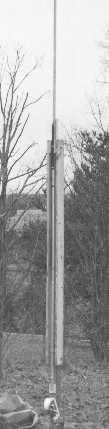
Based on tests, I reached the conclusion that the tilt-over mast could barely support its own weight when the assembly was horizontal. As a demonstration, I mounted a very light 10-meter Moxon beam to the top of the mast and winched the assembly to the horizontal. Photo 7 shows the result. Perhaps the assembly might have been lifted to the vertical once or twice, but for semi-regular raising and lowering, the mast requires additional support.
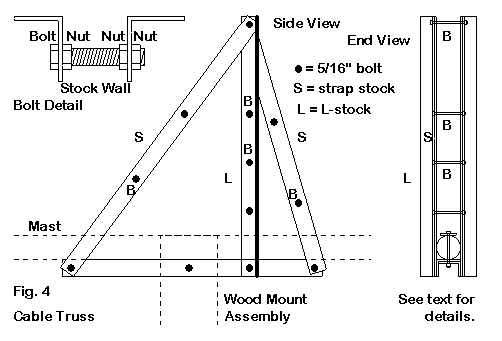
The support system is a lifting truss and cable. 3/16″ galvanised steel cable provides one part of the trussing system. A steel triangle, shown in Photo 8 and Figure 4, provides the support for the cable. The vertical portion of the assembly consists of two 2′ pieces of the same Steel L-stock used for the mast support. These vertical pieces are positioned just forward of the mast pivot position with just enough clearance to pass by the top of the wood cradle. The angled pieces are 3.5′ and 2.3′ pieces of 1/8″ thick steel perforated strap. All of these pieces joined at the top with a 5/16 by 2.5″ bolt. This bolt also acts as the crossing point for the cable.
The bases of the three pieces on each side of the mast are bolted to the U-channel that supports the mast. Each bolt passes all the way through the U-channel, with inside split- ring lock washers and nuts on the inside. Hence, they lock the sides of the U-channel from collapsing inward. The top bolt of the truss support uses the same system to ensure that the two sides maintain their positions. In addition, nuts, bolts, and lock washers are added along the straps and the vertical L-stock to add to the system’s rigidity.
On the top bolt, I added a piece of tubing so that the cable would not rest on the screw threads. When I assemble the system, I cross-tie the cable to the top bolt with cable wraps. Their sole function is to prevent the cable from falling off the assembly while one or the other end is loose. I simply cut them off during disassembly (and collect them, since they do not do lawn mowers much good).
Using the Tilt-Over Mast
The description of the structure of the double-knee tilt-over mast has described most of the assembly and raising features. Disassembly is simply the reverse procedure. However, using the mast requires just a word–mostly of caution.
Once the total mast has been assembled and tested without an antenna, perform a final inspection before mounting the antenna to the top of the mast. Be certain that the winch is locked and that the truss cable is properly fastened at each end and that it cross the top of the triangle support well centered on its covered bolt. Mount the antenna securely, with suitable tests to ensure that it will not slip when the mast is vertical.
When raising the loaded mast, be certain that you have the mast locking wing-nut at hand. However, during either raising or lowering, keep one hand securely on the winch handle and the other ready to ensure that the safety lock engages should any slippage occur. This measure is especially important during lowering, when the lock requires a change of position to stop downward motion. Position yourself away from the weighted side of the mast. Wearing a padded jacket, eye protection, and even a hard hat are also wise, although probably inconvenient.
Be certain that the antenna support device to be used at ground level is properly positioned to catch the mast–but not the antenna itself. If lowering the mast, be sure that all guys have been released and dressed so as not to interfere with the mast tilting. If test or operating equipment is to be used while the antenna is vertical, clear the gear from the area during mast operations. In fact, police the area to ensure that there are no materials over which you might trip while your eyes are on the system. I have no children–at home or as neighbors. If you do have some, protect them from the system.
Maintenance
The antennas lifted so far have all been less than 20 pounds, including the boom-to-mast plate and U-bolts. I would not recommend much more weight be placed on the system than this, since we must multiply the weight times the distance from the pivot to appreciate stresses involved. I have considered installing a small TV rotator, but decided against the added weight until the system has proven durable.
Maintenance of the system has two facets. First, every time I disassemble the pieces for storage, I check and clean everything. The winch rope is extended and inspected. The winch itself is cleaned, oiled, and the handle tightened. Hardware and wooden pieces are inspected for wear. The truss also undergoes inspection and spot-recoating. Its hardware is checked for tightness. The truss cable is cleaned and lightly oiled for storage. The mast sections are checked for stress cracks, rust, wear, and curvature.
The second facet of maintenance is to replace wearing items before they wear out. Every piece of the system is a relatively inexpensive home center item. The smallest question mark about the soundness of a piece results in a replacement. (So far, I have only replaced one of the added short inner boards at the pivot point, due to a crack in the board that I did not initially see.)
One of the design goals was to use parts that I could replace whenever they show signs of wear. Given the type of use to which I put this assembly, the three facets of inspection, maintenance, and replacement become part of a single package. Since the assembly is in storage for longer periods than when in use, I simply inspect each and every part before and after each session.
Among the signs of wear are the following:
- 1. Deformation of the masts, both along their length and at hardware attachment points.
- 2. Signs of metal cracking or fatigue at holes and hardware attachment points.
- 3. Wear on hardware, especially that used as pivots or as stress points.
- 4. Wear or other degradation of wood elements and their drilled holes.
- 5. Cable and rope condition, including stay cable stretch.
- 6. Winch operation, including locking.
This short checklist does not include some general precautions. First, use stainless steel or galvanized hardware everywhere possible. Use stainless steel for pivot bolts (since pivot wear will remove galvanization). Any other steel pieces must be primed and coated to prevent rust.
Any untreated pieces of wood, such as the centering blocks and the pivot reinforcing plates at the top of the cradle, should be coated with marine varnish. Even the pressure treated wood should have a periodic treatment with a water sealer to slow the inevitable drying. The post should be inspected periodically for condition, especially its verticalness. The treated lumber available at most home centers varies considerably in quality, and it is not always possible to know in advance whether a post or plank will curve with time and use.
These kinds of precautions are second nature with me. Hence, I have felt willing to press the materials to see what I could produce to ease the job of raising and lowering test antennas. The double-knee design has indeed eased the job of setting up and taking down the assembly, and the tilt-over feature has speeded antenna adjustments. With considerable re-engineering, one might create a double-knee tilt-over tower for more regular use. However, with anything tall and especially with anything that tilts, safety must always be the first concern. So I have presented what I use, but with the strong caution not to try to duplicate it. Instead, make your version stronger and safer.
Originally posted on the AntennaX Online Magazine by L. B. Cebik, W4RNL
Last Updated : 19th May 2024